Diaphragm walls are commonly used as retention systems, particularly in constructing basements, tunnel approaches, dams, and enclosures. A diaphragm wall has fewer joints than other retention walls, which increases the water tightness of the wall. Diaphragm walls are commonly employed in the construction of deep excavations due to their exceptional capacity to withstand immense structural loads.
This article discusses the features and construction process of the diaphragm walls.
What is Diaphragm Wall?
Diaphragm wall is one of the best techniques for retaining earth. To prevent the excavation wall from collapsing, a concrete wall is built. Grab or hydrofraise are specialised drilling machines that construct diaphragm or slurry walls. To prevent a local collapse of the drilled wall, bentonite slurry is employed. Drilling continues all the way down to the slurry wall or diaphragm wall’s floor level. The diaphragm wall is first drilled, followed by the installation of the bar, and then the entire drilled portion is concreted to make the concrete wall. A thermal tube is used to cast the diaphragm wall. A tremie tube is a tube used to pour concrete into the excavation’s lower level. The concreting causes the bentonite to rise and be recovered for reuse since concrete has a higher specific gravity than bentonite.
Features of a Diaphragm Wall
Diaphragm walls create a rectangular portion that is built underground. Thus, this is an underground concrete wall. To maintain water tightness and structural stability, these walls are built panel by panel, each linked together.
The thickness of a diaphragm wall can range from 60 cm to 150 cm, and its breadth can range from 2.0 and 3.5 metres. Diaphragm walls can be constructed at depths reaching up to 60 meters.
Environmental Impacts of Diaphragm Wall
- Installation without vibration
- Minimal noise pollution: just engine noise
- Bentonite disposal and dirt removal
- Debris removal, old foundation destruction, and stabilised sand backfill
- A solid, dry, and level work platform
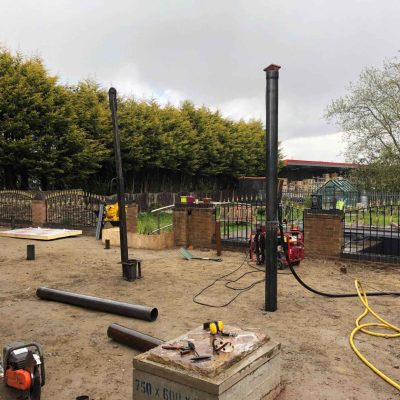
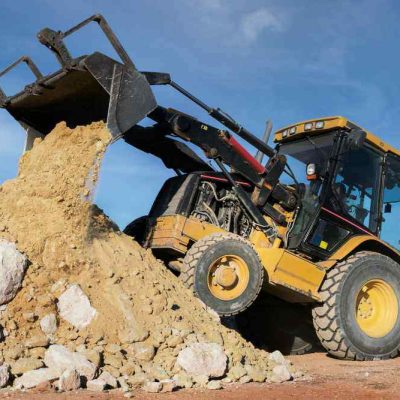
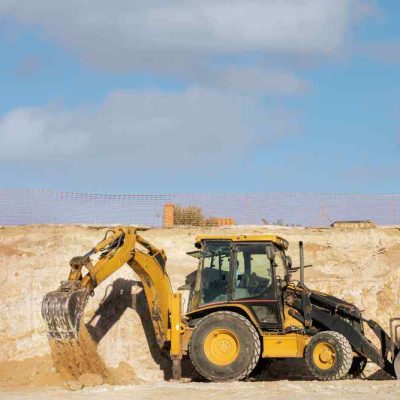
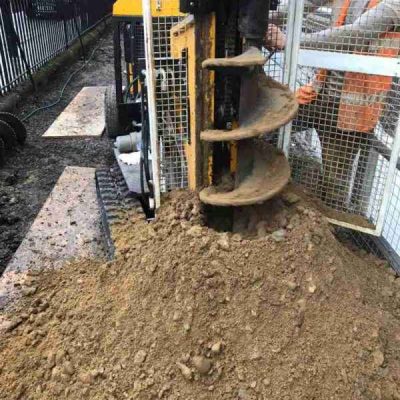
Diaphragm Wall’s Construction Methods
Method 1: Grabbed
For diaphragm wall excavation, two alternative grab methods that are appropriate for wall thicknesses ranging from 600 mm to 1,500 mm are provided.
The grasp penetrates the panel, and the soil is removed in bite-sized pieces. Larger blocks or portions of rock can be removed or moved using adapted grabs or powerful chisels. Verifying verticality can be done by installing measuring systems.
The jaws are moved by a cable system on mechanical grabs. Hydraulic grabs operate with hydraulic cylinders. They operate with less noise and vibration than mechanical grabs and have extremely high closure forces.
Method 2: Cutting
Diaphragm walls can be cut to thicknesses ranging from 500 mm to 3,200 mm using diaphragm wall cutters. Cutters are best suited for depths over 40 metres as they constantly excavate and remove the spoil. Two counter-rotating cutter wheels used in trench cutter operation can be configured to work with a wide range of strata, such as rock. Wheel rotation cuts the material, which is then crushed, combined with slurry, and suction-pumped to the surface.
Diaphragm Wall Construction
There are three main steps of diaphragm wall construction:
- Guide Wall Construction
- Excavation of the Panel
- Wall Concreting
Guide Wall Construction
Two temporary parallel beams are built along the side of the wall to direct the excavation equipment and stabilise the top portion of the wall, known as guide walls. Prior to building the diaphragm walls, guide walls are put in place to help ensure the continuity of the walls and horizontal alignment.
Also, guide walls:
- Assist in marking the positions of the panel
- Avoid soil settling
- Support the steel cages for reinforcement
Having temporary support, such as a guide wall, is vital because soil slurry levels fluctuate considerably. The type of surface soil affects the guide wall’s construction size. If the area’s water table is too high, a guide wall is built above ground level to direct the building.
Excavation of the Panel
Both stability and soil removal are part of this stage. The panel part is dug out using a rectangular excavation tool. A grab or clamshell is utilised to dig the trench in a typical soil. Grab that is suspended by a cable or crane or easily moves into the ground. If a barrier is encountered, it is removed with the grasp and broken with a gravity hammer.
The aforementioned process must be carried out with sufficient excavation support; otherwise, the sides of the trench could collapse. The bentonite slurry is used to protect the sides. The slurry also aids in creating the lateral pressure necessary to hold the vertical dirt in place.
Wall Concreting
The panel that was dug must now be concreted. The reinforcement cage is first placed inside the trench. If the diaphragm wall is deeper than necessary, two or more steel reinforcement cages must be added to fill the space, and these cages must be lapped.
Tremie pipes are used to pour concrete into the trench once the reinforcement has been laid. Tremie pipe use aids in preventing concrete segregation. The bentonite clay in the trench is replaced by the poured concrete. Bentonite is replaced throughout the concreting process because it has a lower density than concrete. The displaced bentonite clay is gathered and recycled.
Last Words
Diaphragm wall has become a very popular method of the retention system. Many commercial and infrastructure development projects use diaphragm walls as a critical component because they provide a dependable construction method at a substantial depth and with incredibly high load-bearing capacities.